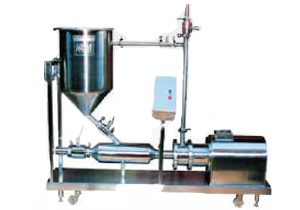 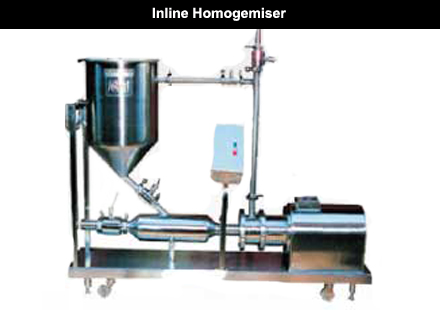 |
|
In
Inline agitation
system,
the possibility
of materials
–
Liquid or
Solid passing
through
it, without
subjected
to intense
hydraulic
and mechanical
shear actions
is zero.
Here suction
pipe (inlet
pipe) is
centrally
mounted
& outlet
is radially
mounted
, therefore
it is physically
impossible
for any
material
to pass
from inlet
to outlet
without
exposed
to agitation.
The stator which surrounds rotor is available with various type of opening i.e. round, square, rectangular & with perforation also so that all the critical demand of Mixing, Emulsifying, Disintegration & Dispersion of solids, suspension can be met out by same equipment.
|
The machine
is versatile
& has
completely
revolutionized
the traditional
mixing techniques.
Here close
tolerance
of rotor
with the
stator produces
high hydraulic
shearing
& mechanical
action that
ensures
that material
entrapped
between
rotor &
stator is
subjected
to tremendous
shearing
actions
each minute.
Fluid
Mixing Mechanisms:
In terms
of mechanical
mixing mechanisms,
a number
of actions
are employed
by different
types of
mixers to
create different
effects
for particular
process
results.
For distributive
action,
swirl created
by rotating
parts causes
laminar
thinning
of the material
interfaces,
thereby
increasing
volumetric
combination
of the materials.
A repeated
cutting
and folding
action of
the mixture
also increases
the distribution
of different
material
components.
The effectiveness
and efficiency
of a mixer
in distributive
mixing is
therefore
a function
of how the
machine
interacts
with the
fluid in
a geometric
sense.
Conversely,
the effectiveness
and efficiency
of a mixer
in dispersive
mixing is
a function
of how the
machine
interacts
with the
fluid in
a stressing
sense. For
most materials,
the higher
the stress,
the smaller
the resulting
particles
or droplets
in the mixture.
However,
another
very important
consideration
is the uniformity
of the stress
field. Without
a reasonable
uniformity,
it is impossible
to guarantee
that the
same stress
is applied
to all parts
of the fluid.
This would
result in
a wide range
of final
droplet
or particle
sizes rather
than a narrow
range obtained
with uniform
stressing.
One or more
of the three
primary
stressing
mechanisms
are used
in most
fluid mixers.These
mechanisms
are:
Inline
Mixers:
Usually
called
"high-shear
mixers",
are the
most common
form of
Dispersing/Homogenising/
Emulsifying
mixer.
By placing
a form
of closely-fitting
shroud
around
a high
speed
impeller,
it is
possible
to create
a shearing
action
between
the blades
and stator
shroud.
As material
is centrifugally
pumped
through
the mixing
head,
some of
it will
see this
high shear
zone and
experience
shear
stressing
that results
in dispersive
mixing.
Where
small
or uniform
dispersions
are required,
material
must be
cycled
through
the head
many times
to ensure
statistically
that all
of the
material
has passed
through
the high
shear
zone at
least
once.
Pumping
Action
:
Because
of indigenous
design
& rotor
operating
at very
high speed
in close
clearance
with stator
draws
the material
in & imparts
mechanical
& shearing
actions.
Inline
Homogenizer
facilitates
high volume,
non positive
action
which
is sufficient
to transfer
the material
without
any supplementary
pumps
but in
some cases
because
of high
viscosity,
vertical
lift or
length
of pipe
line ,
the flow
rate may
come down
below
the anticipated
value,
In that
case it
is supplemented
by an
auxiliary
pump installed
in the
system
which
pumps
the liquid
without
reducing
the homogenising/emulsifying
efficiency
of the
system.
End
Connection
:
The inlet
& outlet
are normally
fitted
with DIN,
Tri Clover/
Sanitary
Screw
fittings
but other
Modes
of fittings
can be
provided
on request.
Sealing
:
Single
mechanical
seal with
Carbon,
silicon
carbonized
phase
combination
is provided.
Special
single
or double
sealing
is also
available
for conditions
& process
which
demand
it eg.
Latex
, Abrasive
solids.
Applications
of Inline
Homogeniser
Emulsifier
Inline
emulsifier
is successfully
used for
the following
processes
:
Recirculatory
Processing
:
There
are certain
processes
which
demand
higher
degree
of homogenization,
dispersion,
comminution
& but
to attain
that level,
single
passage
of material
through
Inline
is not
sufficient
to reach
that degree
, in that
situation
, it is
more useful
to pass
the product
several
times
through
the same
machine
by means
of recirculation.
The above
process
is normally
adopted
in producing
emulsion
of Oil
& Water.
Oil ,
which
is lighter
than water
is charged
in the
holding
vessel
& water
is added
into the
pipe line
between
vessel
outlet
valve
& Inlet
of Inline
Emulsifier.
This mix
is immediately
sucked
into the
head of
emulsifier
& there
mixing/
emulsification/
homogenization
takes
place
. This
mix is
then sent
into the
vessel.
This process
is repeated
till achievement
of perfect
emulsion.
Where
viscosity
is very
high or
vessel
size is
large,
it is
recommended
to go
for Batch
type mixer
along
with Inline
Mixer.
Premix
Process
:
In this
process,
all ingredient
are mixed
in a holding
vessel
with some
agitator
& a single
passage
through
the inline
smoothens
the lumps
and homogenize
a suspension
or emulsion.
Inline
Mixer
is currently
in use
in the
industry
listed
below
& this
gives
a new
horizon
for this
exceptional
machine
to validate
its results.
- Creams
- Dairy
& Confectionary
items
- Beverage
& Brewery
- Paper
coating
- Pharmaceuticals
- Pesticides
& Insecticides
- Paints
- Natural
Herbal
Dye
Capacities
Available:
3 Hp models
to 25 Hp
models |
|